Customer testimonial: 95 % reduction in received emails
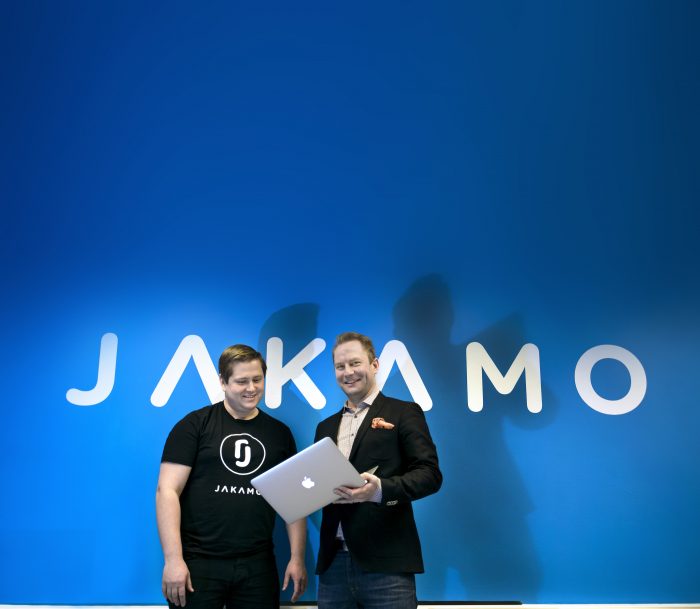
This article has been published in Finnish top tech-business magazine Tekniikka&Talous on 10 February 2017.
JAKAMO IS READY FOR THE LEAP
Jakamo, the collaboration platform designed for manufacturing companies, has progressed to the point where the next step is strong growth. This year, Jakamo is aiming for doubling or even tripling turnover.
In order to achieve faster growth, the Seinäjoki-based startup in Finland, is updating its business model. “An essential part of our growth strategy is to improve Jakamo’s integration possibilities into our customers’ existing IT systems, such as ERP systems. At the same time we move to a new partnership model”, says Jakamo’s CEO Anssi Uitto. In the partnership model, Jakamo offers software developers the Jakamo platform, on which the partner companies can encode company-specific applications.
Tekniikka&Talous magazine asked three Finnish industrial companies experiences in using Jakamo. Based on the feedback, Jakamo’s connection to existing IT infrastructure is a welcomed development.
“Jakamo should develop the integration into ERP systems. That way Jakamo could better integrate into the daily activities. Now, it is still a little stand-alone program”, says ABB’s R&D Manager Kari Salo. In ABB Transformers, Jakamo enables communication with subcontractors related to design issues. E-mail traffic has decreased by as much as 95 % in subcontracting projects. Open collaboration has improved project management. “If there is a need to replace the head designer, the deputy can immediately catch up to the project, and there is no need to send dozens of emails to get started”, Salo says.
Komas, the metal industry subcontractor, utilizes Jakamo with subcontractors and material suppliers as a communication tool as well as a channel for claim handling. Jakamo is also utilized in the management of RFQ processes and supplier audits. “The lead time of RFQ processes are shortened and the amount of related e-mails decreased by more than half. The follow-up of RFQ process is also much easier”, says Purchasing Manager Eetu Pakkanen from Komas.
Valmet has implemented Jakamo widely in the corporation as a development tool. Jakamo developed a customized continuous improvement application for Valmet. It was first adopted with Valmet’s largest boiler manufacturing subcontractors in China and Eastern Europe a year ago. The solution will also expand the use of smaller partner companies.
“Although it is still early to assess the impact of Jakamo, my own gut feeling is that it has affected positively on the quality of the production. The progress in quality costs has been good”, says Valmet Production Manager Jussi Sinisalo. Sinisalo states that becoming a world-class player, would require Jakamo to integrate their services into other enterprise systems. “In larger companies there is IT infrastructure, which has been developed for a long time into the company’s needs. The benefits of Jakamo can be realized when it is cost-effectively connected to existing systems”, Sinisalo states.
Jakamo is a tool for quality monitoring and suppliers are also able to give development initiatives through the same tool. “The subcontractors have often good proposals, which often have significant influence to the production costs. When we are able to show the development ideas, it’s easier to execute the change”, Sinisalo says.
In the future, Jakamo will no longer make company-specific applications, those will be done by the partner companies. Jakamo will focus on the development of the core software. During this year, the company will concentrate especially on the integrations to the most significant ERP systems. Broader integration projects naturally produce better income for Jakamo. “The integration project will lead to better one-time compensation, which all parties benefit”, says Anssi Uitto.
The CEO of Jakamo Anssi Uitto and the other Co-founder Jarl Matti Anttila. Photo: Matti Hautamäki